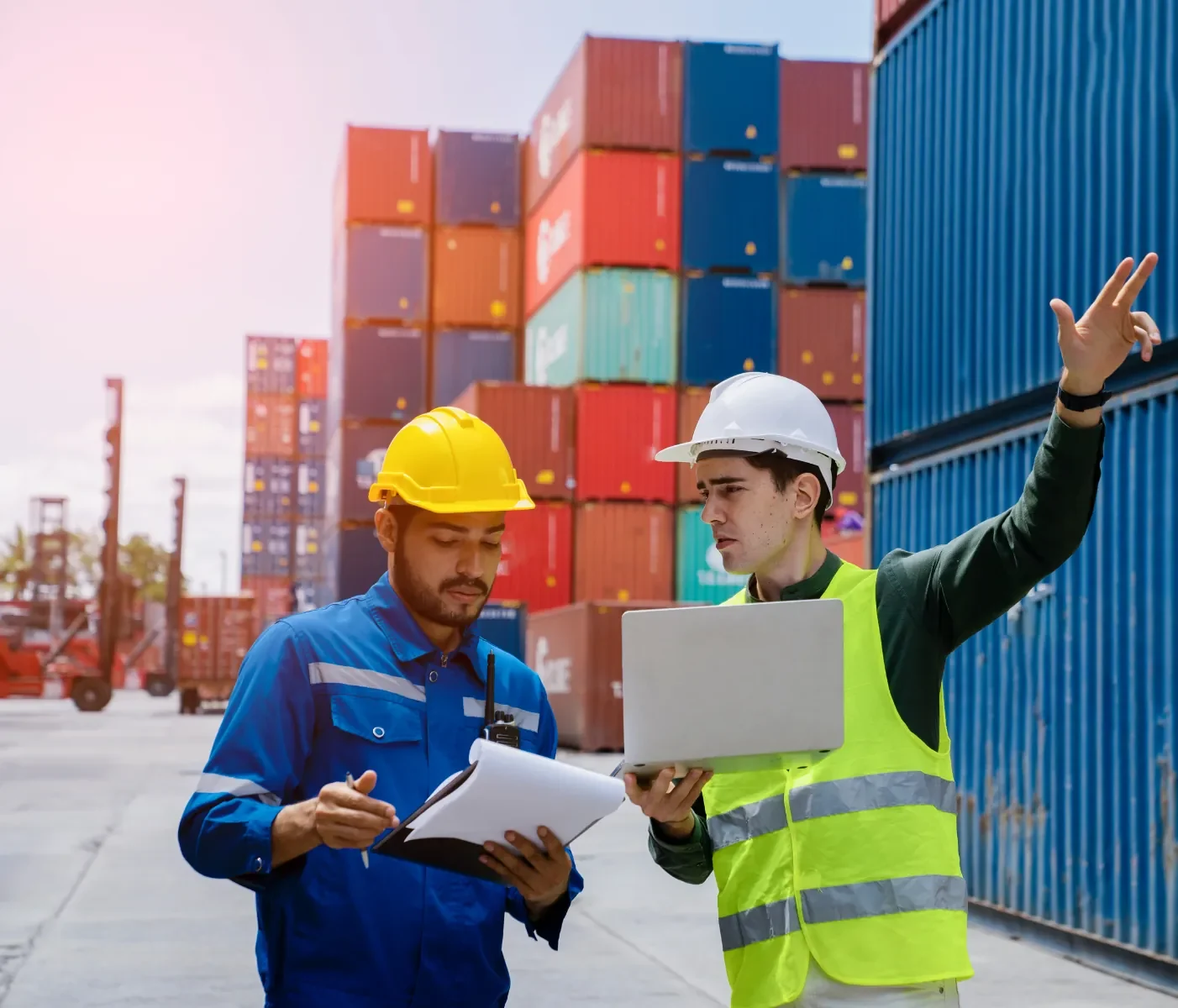
CSRD and supply chain: What purchasing needs to consider
The CSRD with its ESRS standards is not only a lot of work, it also has a major impact on companies: This is because you have to make extensive ESG disclosures – and not only look at your own company, but also at the supply chain. Read here what purchasing departments need to consider and what opportunities and risks arise from the EU directive.
The CSRD (Corporate Sustainability Reporting Directive) has applied to the first companies since January 2024, and others are gradually being added.
Ultimately, around 50,000 companies in Europe will be obliged to publish a report with comprehensive information on ESG (environmental, social and governance) issues.
The ESRS, the European Sustainability Reporting Standards, were also introduced with the CSRD.
For the first time in the EU, they provide a standardized framework for the preparation of a sustainability report – in simple terms: which ESG information is required and in what form it must be reported.
It is important to note that the reporting obligation not only relates to the company itself, but also extends to the entire value chain. In this blog post, we look at the upstream value chain – i.e. the supply chain.
And this is where companies subject to CSRD reporting requirements can quickly run into problems: they need a lot of information from their suppliers and the data situation is often inadequate – according to the Bertelsmann Stiftung’s Sustainability Transformation Monitor 2024.
With VERSO, you can master this challenge.
Our Supply Chain Hub creates transparency in the supply chain and enables you to analyze risks, develop targeted measures and comply with reporting obligations.
We will now take a closer look at these disclosure requirements within the framework of the CSRD and the impact on purchasing.
CSRD and supply chain: What needs to be reported?
The CSRD demands a lot from companies: the ESRS comprises around 1150 data points and over 100 of these relate to the supply chain.
Purchasing is therefore an important player in the reporting process.
The information involved can be roughly summarized as follows: The ESG report must contain information on environmental and social IROs (impacts, risks and opportunities) in the supply chain as well as measures related to the IROs.
If your company is affected by the LkSG, you will probably recognize some disclosure requirements and can realize synergies: This is because some BAFA requirements overlap with the ESRS.
But what does this mean in detail?
To answer this question, let’s take a closer look at some ESRS standards and clarify how they relate to the supply chain.
ESRS E1 – the climate protection standard
The name says it all: ESRS E1 is about climate protection – in your company and in your supply chain. Your company must therefore not only disclose its own greenhouse gas emissions, but also the CO2 emissions in the upstream and downstream value chain – i.e. in Scope 3. Incidentally, the majority of companies generate the most emissions in this category.
E1 also requires companies to set themselves climate targets.
Transparency about the targets and measures of their own suppliers is crucial in this respect.
ESRS E5 – Resource utilization and circular economy
The supply chain naturally plays an important role in ESRS E5, as many resources are obtained or processed here.
For example, the CSRD asks for:
- Measures to avoid the generation of waste
- Resource utilization
- Measures to promote the circular economy
- Cooperation or initiatives to improve the recyclability of products and materials
ESRS S2 – Workforce in the value chain
The fact that the ESRS S2 also relates to the supply chain and entails disclosure obligations is already in the name, so to speak.
Among other things, the CSRD is concerned here with how your company fulfills the due diligence obligations.
This means How do you Ensure compliance with human rights, labor standards andgood working conditions at suppliers ?The CSRD does not require much more than the LkSG. You should also show whether there is a complaints management or whistleblower system for workers in the supply chain, how you handle complaints and resolve any problems raised.
ESRS S3 – Affected communities
The ESRS S3 addresses the impacts that your company’s operations, products or services, and upstream and downstream value chains have on “affected communities”.
This refers to people and groups who live or work in the same area as a company.
The standard also explicitly refers to impacts on indigenous peoples.
Impacts can arise, for example, from truck transportation, the extraction of raw materials or controversial land use.
ESRS G1 – Company policy
With regard to the supply chain, your company must
ESRS G1, your company must disclose the following:
- Management of relationships with suppliers, payment practices, in particular with regard to late payments to small and medium-sized enterprises
- Strategies for detecting and preventing corruption and bribery, including training for suppliers
However, you do not have to provide information on every standard in your CSRD report.
This depends on whether a topic is material for your company.
VERSO offers you an AI-supported materiality analysis here.
In our white paper “All information on the ESRS” you will also find further detailed information on the European standards, in particular on the transition periods.
CSRD and the supply chain: opportunities and risks for procurement
The CSRD is a major challenge – we can’t hide that and we don’t want to.
With almost 1200 data points, ESRS reporting is a mammoth task.
It is complex and resource-intensive.
But with the right support, you can manage it – we will be happy to assist you with the sustainable transformation.
What’s more, the CSRD doesn’t just end with a sustainability report.
The fact that your company is systematically addressing the issue of sustainability opens up great opportunities.
The double materiality analysis and reporting will make opportunities and risks in the supply chain more visible.
This enables your company to address these in a targeted manner.
Sustainability requirements can trigger innovations, such as the use of environmentally friendly materials or the optimization of logistics processes.
Many customers also tell us that the reporting process has enabled them to get to know their suppliers even better.
The increased transparency ensures better and more sustainable supply chain practices.
By working closely together, you strengthen long-term partnerships and thus improve the stability and efficiency of the supply chain.
The reporting process promotes digital development.
Software specialized in CSRD, LkSG and CBAM requirements helps monitor the supply chain and ensures compliance with legal requirements.
It can collect and process the necessary large volumes of data.
How does CSRD influence purchasing and the supply chain?
CSRD has a major impact on purchasing and requires a high degree of transparency and responsibility.
Your company must collect and provide detailed information and comply with legal due diligence obligations in relation to environmental and social standards.
This includes a new assessment in the purchasing process to ensure that suppliers comply with sustainability requirements.
So you need to be even more careful about who your company does business with.
Teamwork is also required when it comes to climate change.
Climate change and extreme weather will affect us all.
That’s why we need to act together to slow down climate change and reduce its impact.
Climate protection measures must not stop at the gates of your own company: Together with your suppliers, you can implement initiatives that help reduce greenhouse gas emissions.
You can find specific tips for decarbonizing your supply chain in the blog post “Why is climate protection in the supply chain relevant?”.
How VERSO supports you in implementing the CSRD
VERSO offers you the all-in-one package for implementing the CSRD.
The EU directive makes the topic of sustainability in the supply chain even more relevant, as companies must now also report robustly on sustainability activities in the supply chain.
The VERSO Supply Chain Hub helps procurement to record the necessary data in the supply chain, monitor suppliers and provide the required reporting key figures with minimal effort.
We round off the package for implementing your CSRD obligations with additional software solutions and consulting services.
With VERSO, you can carry out an AI-supported materiality analysis.
In the ESG Hub, you collect all relevant data and create a meaningful sustainability report.
The Climate Hub supports you with your carbon footprint and decarbonization strategy.
And in the VERSO Academy, you will acquire the necessary knowledge about CSRD and ESRS.
* This information is summarized editorial content and should not be construed as legal advice. VERSO accepts no liability.
This might also interest you:
Subscribe to our newsletter!
Sign up and receive regular news about:
- Pragmatic all-in-one solution for ESG reporting, climate and supply chain management
- Individual advice from the VERSO experts
- Developed with expertise from 12+ years of sustainability management
- Trusted by 250+ customers